Home ⁄ Case Studies ⁄ Design & Build a Robotic System
Design & Build a Robotic System
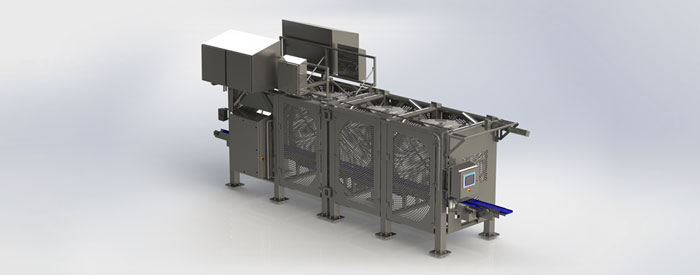
Challenge:
Stainless Steel Solutions was asked to modify a robotic system installed at a food processing plant. In addition to this modification, the customer was unsure if they wanted to continue to use their current system for future robotic cells. Stainless Steel Solutions was challenges to develop a new robotic system that consisted of a completely different system but also met additional criteria requested from the customer. As the project progressed, the system was modified and upgraded, and together we were able to reach the initial goals.
Samples of some of the requirements were as follows:
- Structural
- Stable enough to support the robots
- Minimal movement between the vision system and robots
- Designed to be assembled and tested at the stainless facility as well as easily broken down, transported and installed at our customer’s facility
- Product safety
- Using guarding material that will not chip / break off and contaminate product unless detectable (ex: metal or X-ray detectable)
- 360° access for cleaning inside the framework o Minimal floor mounting locations
- Follow standard FDA / USDA guidelines
- Operator Safety
- Guarding that allows visual inspection of the system while operating but is quickly removable for maintenance access.
- Elimination of pinch points and other potential hazards
Solution:
The customer purchased the robotic and vision components and had the items shipped to Stainless Steel Solution’s facility. We worked together with safety, sanitation, end users and vendors of the robotic system to develop a concept design. Our engineers used SolidWorks to create a solid model of the design, and eDrawings to share the solid models with all members of the project. This approached allowed everyone involved to quickly understand the design intentions and offer their suggestions.
The final design was a modular assembly consisting of four main assemblies. The main portion of the frame was built as two self-supporting structures. One of the frame structures included two additional structures to cantilever the robot controls above and away from the robots to allow more open operating area, robot maintenance, and minimization of floor contact. For delivery to the customer, these four sections were easily separated, internal items secured, and it all fit on a standard flatbed semi-trailer. With the assistance of a rigging company, Stainless Steel Solutions installed and had the system ready for final electrical connections by the end of a weekend. Additional support and development of both systems continue to this day. Stainless Steel Solutions is dedicated to the long term success of our projects.
Benefits:
- Additional access for sanitation
- Improvement on sanitary design
- Increased production
- Increased control over non-conforming product
- Data logging and monitoring capabilities
- Reduction in employee contact
- Food safe guarding while keeping visual inspection capabilities
- Reduction in the total floor space consumed by system
- Modular design allows for additional options in the future